100% Original Factory Fulvic Acid 479-66-3 - 50,000 Tons/year Disc Granulator Production Line – Exceed
100% Original Factory Fulvic Acid 479-66-3 - 50,000 Tons/year Disc Granulator Production Line – Exceed Detail:
Our disc granulator production line mainly produces compound fertilizer with an annual output of 50,000 tons. In general, compound fertilizer contains at least 2 elements of three nutrients (nitrogen, phosphorus, and potassium). With features of high nutrient content, few side effects, and good physical properties, compound fertilizer plays an important role in balancing fertilization, improving fertilizer application efficiency and promoting high and stable yield of crops, our pan granulator compound fertilizer production line is specially designed for fertilizer manufacturers who has a large output requirement. This fertilizer production line can manufacture NPK fertilizer, DAP and granulate other materials into compound fertilizer particles. The process technology of this fertilizer plant is advanced, effective and practical. All fertilizer equipment are compact, high-automatic and easy operation, which is more convenient for mass compound fertilizer production.
Advantage
1.All fertilizer machines adopt anti-corrosion & wear-resistant materials.
2. Adjustable capacity according to customer’ requirements.
3. No waste discharge, energy saving and consumption reducing, environment protecting. Stable operation, simple to maintain.
4. This fertilizer production line can produce not only compound fertilizer with high, medium, and low concentration, but organic fertilizer, inorganic fertilizer, bio fertilizer and magnetizing fertilizer etc. Pan granulator is with high granulation rate.
5. The 50,000 tons/year compound fertilizer production line is high returns on investment, low risk, and payback time is short.
6. With compact layout, the complete set of fertilizer equipment is scientific and reasonable, and advanced in technology.
7. Wide adaptability of raw materials, suitable for the granulation of compound fertilizers, pharmaceuticals, chemicals, feed and other raw materials.
The whole line includes Disc feeder (putting the materials in the tank) → Disc mixer (for stirring the raw materials)→ chain crusher (for crushing)→ Disc granulator (for granulating)→ rotary drum dryer(for drying) → rotary drum cooler (for cooling) → rotary drum screen (for screening the finished and unqualified products)→ finished products warehouse (for storage)→ automatic packager (for packaging)→ belt conveyor→ dust settling chamber→ heat exchanger
NOTICE: This production line is for your reference only.
Working principle
The granulation technological process of compound fertilizer production line can be usually divided into:
1. Material Batching Process
First, raw materials are allocated in strict accordance with the proportion. The raw materials includes urea, ammonium nitrate, ammonium chloride, ammonium sulphate, ammonium phosphate (monoammonium phosphate, diammonium phosphate, single superphosphate, and coarse whiting), potassium chloride, potassium sulfate and etc. The strict allocation ratio of raw materials guarantee the high fertilizer efficiency.
2. Materials Stirring Process
Raw materials are mixed together in flat disc mixer which can stir materials evenly to improve the fertilizer efficiency.
3. Crushing Process
The chain crusher machine will crush the large material into small pieces which can meet the demands of granulation. Then the belt conveyor will send the materials to pan granulator to granulate.
4. Granulating Process
Disc fertilizer granulator adopts arc disc angle structure. The granulation rate can reach above 93%, which has one of the best granulation ratios among all fertilizer granulators. Utilizing the continuous counter-rotating of the equipment and spraying device to drive raw materials rolling in the disc. It can produce uniform and nice appearance granules. Pan granulator is an indispensable machine in compound fertilizer production line.
5. Drying & Cooling Process
After granulating, the granules need to be dried. Belt conveyor transport the granules to the rotary drum drier. The drying machine removes moisture from the particles to increase the intensity of granules. Thus, it is convenient for storage.
After drying, the temperature of fertilizer granules is too high to agglomerate. Thus we need to cool the fertilizer with the use of rotary drum cooler machine. After being cooled,fertilizer granules are easy to package, preserve and transport.
6. Particle Classification Process
Fertilizer should be screened by rotary drum sifting machine after being cooled. Qualified products will be sent into the finished product warehouse by belt conveyor or can be packed directly. Unqualified granules will be re-granulated.
7.Product Packing Process
Packing is the last process in compound fertilizer production line. Full-automatic fertilizer packager is utilized to package finished products. With high-automatic and high-efficiency, it not only achieves accurate weighing, but accomplishes the last technique process excellently. Customers can control the feeding speed and set the speed parameter wilfully.
Product detail pictures:
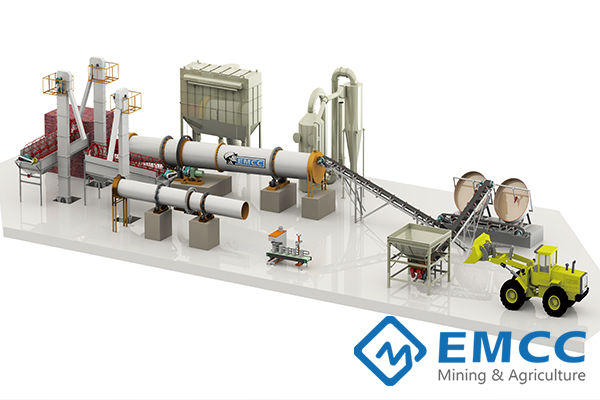
Related Product Guide:
Liquid Fertilizers Market By Current Scenario with Growth Rate | 2016 – 2024 | Fertilizer Granulating Machine
South Jersey sewage plant makes energy from wind, solar — and meatball grease | Fertilizer Wet Mixing Granulator
We support our purchasers with ideal high-quality merchandise and significant level company. Becoming the specialist manufacturer in this sector, we now have received loaded practical encounter in producing and managing for 100% Original Factory Fulvic Acid 479-66-3 - 50,000 Tons/year Disc Granulator Production Line – Exceed, The product will supply to all over the world, such as: Libya , Algeria , Mecca , There are advanced producing & processing equipment and skilled workers to ensure the merchandise with high quality. We've got found an excellent before-sale, sale, after-sale service to ensure the customers that could rest assured to make orders. Until now our merchandise are now moving on fast and very popular in South America, East Asia, the Middle east, Africa, etc.

Timely delivery, strict implementation of the contract provisions of the goods, encountered special circumstances, but also actively cooperate, a trustworthy company!
